Get premium membership and access questions with answers, video lessons as well as revision papers.
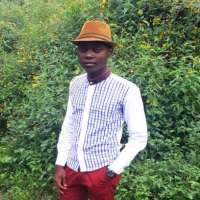
a) Quality circles
This is a quality control technique, which originated in Japan. It involves the use of committee of workers that analyzes and solves the quality problems of various departments in the organization.
The quality groups are established in every department and trained on problem solving by use of statistical quality control and other process.
They are encouraged to make important inputs to key decisions affecting their activities.
Quality circles are not permanent committees and comprise small groups of about eight to ten employees and membership is rotated between members of the department/production plant.
They meet together on a regular basis to discuss day-to-day issues such as quality, productivity and safety, with the object of:
i. Making improvements
ii. Organising their implementation
b) Basic characteristics of quality circles.
i) Membership is voluntary, but usually consisting of a number of shop floor employees and a foreman or supervisor, or may consist of a mixture of skilled and unskilled employees together with one or two shop-floor specialists such as quality engineers and inspectors.
ii) Each circle selects its own leader, and usually the organisation concerned provides training for such leaders in appropriate subjects(discussion leading, quality control, etc)
iii) Members are trained in problem solving, in statistical quality control, and in working groups. A facilitator may work with the group but efficiency experts are usually excluded from the team. The team members participate actively in solving work-related problems.
iv) Although initially the groups were trained in the analysis of quality problems, currently other problems, such as cost reduction, workshop facilities improvement, safety problems, employee morale, pollution control and education of employees, are also dealt with.
v) The employees are given the tools, group support, and opportunities to nip problems in the bud.
vi) Each QC is responsible not only for recommending solutions but also for actually implementing and evaluating results.
vii) The QC members present their results, reports and deliberations for consideration by management.
viii) They usually implement proposals accepted by management.
c) How do employees benefit from participating in quality circles?
i) Greater awareness of shop-floor problems by circle members/Increased knowledge in area of work
ii) Greater confidence in tackling problems and generating solutions on the part of circle members as the members are trained on this.
iii) Improved productivity and/or quality because the circles provide checks among the members.
iv) Improved motivation and self-esteem on the shop-floor because of employee involvement in solving organizational problems/concerns
v) Improved communication skills.
vi) Skills development, particularly problem-solving skills.
vii) Employees become agents of change making the change process easier.
Kavungya answered the question on April 30, 2021 at 06:47
- List the shortcomings of using Maslow’s Hierarchy of Needs Theory as a motivational tool.(Solved)
List the shortcomings of using Maslow’s Hierarchy of Needs Theory as a motivational tool.
Date posted: April 30, 2021. Answers (1)
- Absenteeism and low morale are apparent in the accounting department of XYZ Limited, in which you are employed. Your superior knows that you are a...(Solved)
Absenteeism and low morale are apparent in the accounting department of XYZ Limited, in which you are employed. Your superior knows that you are a student and have heard of Maslow’s Hierarchy of Needs Theory. However, your superior is also aware that, although the theory has some relevance to motivational techniques, it has substantial limitations.
Using appropriate examples, explain Maslow’s Hierarchy of Needs Theory.
Date posted: April 30, 2021. Answers (1)
- Exactly what constitutes the management task is often unclear or misunderstood.
Explain the five main duties of a manager, according to the writer Henri Fayol.(Solved)
Exactly what constitutes the management task is often unclear or misunderstood.
Explain the five main duties of a manager, according to the writer Henri Fayol.
Date posted: April 30, 2021. Answers (1)
- What are the desirable elements of a sound promotion policy in an organization.(Solved)
What are the desirable elements of a sound promotion policy in an organization.
Date posted: April 30, 2021. Answers (1)
- It is essential that new employees go through a period of orientation and training before formally settling in their positions.
What benefits can a company derive...(Solved)
It is essential that new employees go through a period of orientation and training before formally settling in their positions.
What benefits can a company derive from a well-planned employee induction and training program?
Date posted: April 30, 2021. Answers (1)
- Planning is an important and persuasive activity in many organizations. Identify and distinguish between various types of plans, which are likely to be found in...(Solved)
Planning is an important and persuasive activity in many organizations. Identify and distinguish between various types of plans, which are likely to be found in an organization which invests substantial resources in the planning process
Date posted: April 29, 2021. Answers (1)
- How can organizational cultures be differentiated from each other?(Solved)
How can organizational cultures be differentiated from each other?
Date posted: April 29, 2021. Answers (1)
- How does an organization’s culture manifest itself?(Solved)
How does an organization’s culture manifest itself?
Date posted: April 29, 2021. Answers (1)
- What is meant by the term culture?(Solved)
What is meant by the term culture?
Date posted: April 29, 2021. Answers (1)
- Evaluation of managers is fundamental to assess whether they are performing as expected.
a) Describe the five major methods of evaluating managers.
b) What are the critical...(Solved)
Evaluation of managers is fundamental to assess whether they are performing as expected.
a) Describe the five major methods of evaluating managers.
b) What are the critical guidelines for effective manager evaluation?
Date posted: April 29, 2021. Answers (1)
- Informal groups exist in organizations to cater for interests and needs of workers. State and explain the merits and demerits of informal groups to a...(Solved)
Informal groups exist in organizations to cater for interests and needs of workers. State and explain the merits and demerits of informal groups to a business organization?
Date posted: April 29, 2021. Answers (1)
- What is the importance of the product life cycle for business planning and budgeting?(Solved)
What is the importance of the product life cycle for business planning and budgeting?
Date posted: April 29, 2021. Answers (1)
- Explain why the formulation of strategy in a non-profit organization may be different from a
profit making organization.(Solved)
Explain why the formulation of strategy in a non-profit organization may be different from a
profit making organization.
Date posted: April 29, 2021. Answers (1)
- The production process is one by which goods and services are brought into existence. Write a brief account of the planning and operating decisions and...(Solved)
The production process is one by which goods and services are brought into existence. Write a brief account of the planning and operating decisions and activities, which the production manager is likely to encounter.
Date posted: April 29, 2021. Answers (1)
- What factors determine the optimum span of management and the number of levels of management in an organization?(Solved)
What factors determine the optimum span of management and the number of levels of management in an organization?
Date posted: April 29, 2021. Answers (1)
- Define span of management.(Solved)
Define span of management.
Date posted: April 29, 2021. Answers (1)
- “The nature of strategic management differs according to the type of organizations.”
Discuss this statement with respect to the following types of organizations:
(a) Public sector organizations....(Solved)
“The nature of strategic management differs according to the type of organizations.”
Discuss this statement with respect to the following types of organizations:
(a) Public sector organizations.
(b) Non-profit organizations.
Date posted: April 29, 2021. Answers (1)
- In order to enhance the chances of a new product succeeding, the company should follow a systematic new product development process.
Highlight the major stages in...(Solved)
In order to enhance the chances of a new product succeeding, the company should follow a systematic new product development process.
Highlight the major stages in new product development.
Date posted: April 29, 2021. Answers (1)
- Describe the marketing strategies a firm should adopt in the different stages of a product’s life cycle.(Solved)
Describe the marketing strategies a firm should adopt in the different stages of a product’s life cycle.
Date posted: April 29, 2021. Answers (1)
- Identify and explain the characteristics of an effective management information system.(Solved)
Identify and explain the characteristics of an effective management information system.
Date posted: April 29, 2021. Answers (1)